Alan Dowds outlines their importance…
Alongside engines, frames are right up there in terms of importance for motorcycles. Over the years we’ve seen hundreds of different shapes, types and stiffnesses, made from a multitude of different materials. Which one’s best? Well, that’s a very good question. Here’s why…
Most of the material design choices on a motorbike are obvious nowadays. Engine crankcases are made of aluminium, as are pistons, blocks, and heads – only a madman would try to make a cast iron head, as happened 60 or 70 years ago. Cranks are steel, as are gears and shafts. Valves are stainless steel on normal bikes, or titanium on performance machines. Wheels and fork outers are almost all aluminium, fork inner tubes are steel, fairings are plastic, and rubber tyres are, er, rubber.
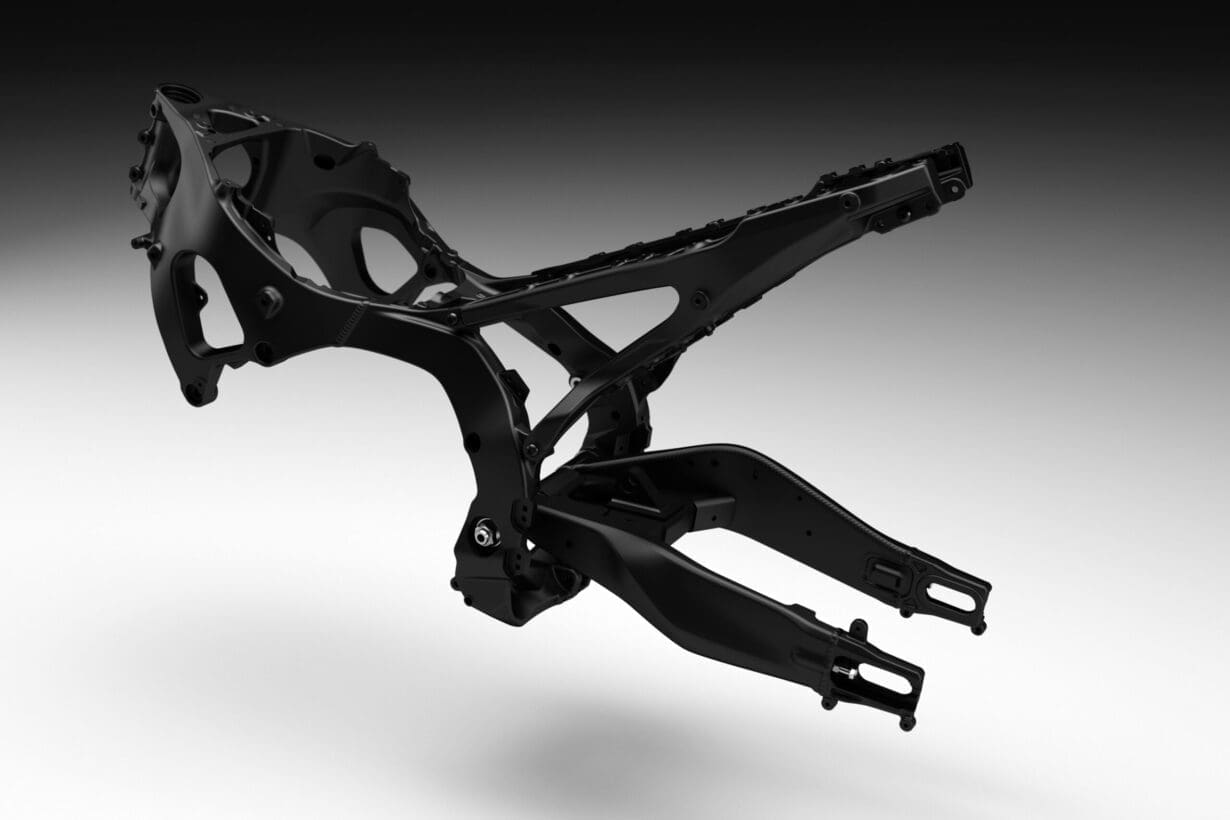
There’s one major component where there’s still a fundamental choice though – the main frame. Almost every bike on the road has a frame made from either steel or aluminium, and the choice varies across the type of machine and cost. Flagship adventure machines like the KTM 1290 Super Adventure and Triumph Tiger 1200 plump for steel tubes, as do most of the cheapest 125 learner bikes out there. On the other hand, almost all current supersports machines have aluminium frames, and that’s gradually becoming true of most standard machinery, too.
So why are there still two options here? The fact is that both steel and aluminium are excellent choices as frame materials – but there are so many factors involved that neither has taken over completely in the way that cast aluminium has for engine cases and wheels, or forged steel for cranks and conrods.
Going back to basics, aluminium is a lot lighter than steel, and resists corrosion far better. Steel is stronger, though, and is also more tough: it has better resistance to fatigue, shock loads and cracking. They’re both fairly inexpensive to buy; steel is generally cheaper and easier to fabricate by welding, stamping or pressing. But aluminium is ideal for casting, with a much lower melting point. Alloying aluminium with other elements like magnesium, silicon, copper and zinc also tweaks its strength and other characteristics to suit. It’s fiddly to weld, though, and needs special gas-shielded techniques.
Up until the 1980s. all motorbikes had steel frames. The technology evolved from bicycle designs in the 19th century: pioneering engineers fitted small petrol motors to the pushbikes of the day, with their narrow-diameter steel tube frames. Over time, the tubes grew in size and strength, and the shape of the frames evolved to cope with increasing power and performance. Pressed steel parts also appeared, made using flat steel sheets stamped out on big presses, then welded together.
The cost and complexity of fabricating aluminium ruled it out, until the Japanese began development at the end of the 1970s. Suzuki’s 1983 RG250 Gamma was the first to appear with a mass-produced aluminium frame, using square-section tubes in a similar dual-cradle layout to a steel tube design. The GSX-R750 launched in 1985 used the same basic set up, and by the end of the 20th century, all the Japanese firms were selling sportsbikes with large, stiff aluminium frames, borrowing tech from the racetrack.
Aluminium’s lightness – it’s around a third of the weight of steel with a third of the strength – meant designers could use more metal, in large hollow beam sections. These were the same weight and strength as a smaller steel tube, but much stiffer, because stiffness is about shape, not material. Remember the school science experiment with a sheet of A4 paper? Roll it into a cylinder, and you can balance a heavy book on top. Unrolled, it can’t even support its own weight. The same idea meant that large aluminium sections, with thin walls, could out-perform steel designs.
Ducati stuck with its steel tube designs, though. Here, the principle is triangulation: use a series of short steel tubes, welded into a network, or trellis layout, and you have a very stiff shape, with fairly light weight. The downside is increased production costs: all those little tubes need to be cut precisely to length then welded together, either by smart artisan welders, or complex robots. It’s much cheaper to have a fabricated twin-spar aluminium frame, or even better, a single aluminium casting.
The extra costs of high-end steel tube frames were okay for a premium brand like Ducati, though, so classic superbikes like the 851, 916 and 999 all used steel trellis frames. And Ducati kept using it as a trademark design in other models like the Monster, Multistrada, Diavel and Streetfighter. Recently, though, even the Bologna engineers have been dropping the trellis frame. The Multistrada, Monster, Panigale, Streetfighter and Diavel have all switched to aluminium monocoque frames, with only the DesertX, Hypermotard and retro Scrambler ranges sticking with steel tubes.

Nowadays, steel frames are becoming restricted to a few use cases. It’s still ideal for small, cheap bikes, where performance and weight aren’t as important as cost and resilience. Big adventure and off-road bikes still work well with steel: its fatigue resistance means it can take repeated hard impacts without cracking or failing, unlike cast aluminium. And firms like Royal Enfield use steel frames to suit the tough road conditions in its home market.
Broadly, though, aluminium is winning out. Modern design and production techniques are giving firms ever more control on how a frame will perform: small, subtle changes to wall thickness on a main frame spar can improve handling and feel drastically. One problem with frames that are *too* stiff is chatter: at high lean angles, the suspension isn’t aligned with the wheel movement when you hit a bump. If a fork leg is leaning over at 45 degrees, any bumps try to bend the fork leg up, rather than compress the springs. Allowing a bit of controlled flex in the main frame can help absorb that movement.
Again, though, there are exceptions. Bimota’s new KB998 has a hybrid frame, with aluminium swingarm pivot plates, bolted to a steel tube trellis front section. That gives the firm the control to tweak stiffness to suit – indeed, the WSBK race team has been able to test completely different front trellis sections at different tracks, to find the best handling solution. It’s not a cheap, or obvious solution – but makes sense for such a small-scale, exotic bike. And it’s further proof that both steel and aluminium are still the best materials for frame designs.