When it comes to chassis development, few folks know more than the legends at Harris Performance. Our pals from Fast Bikes went to town, questioning them on all there is to know about this pivotal, mind-blowing subject. Here’s John ‘Big Mac’ McAvoy’s learnings…
Harris Performance has been building motorcycle frames for the great and the good since 1972, with notable achievements along the way being its ‘Magnum’ frames during the 1980s, a particularly golden era which allowed manufacturers like Harris to take a powerful but bendy Japanese bike and make it much better by replacing the chassis with one of its own. In the 1990s, Harris was one of just two frame builders to be given the right to build frames for Grand Prix teams who could get their hands on a Yamaha YZR500cc V4 engine; the other was French manufacturer ROC.
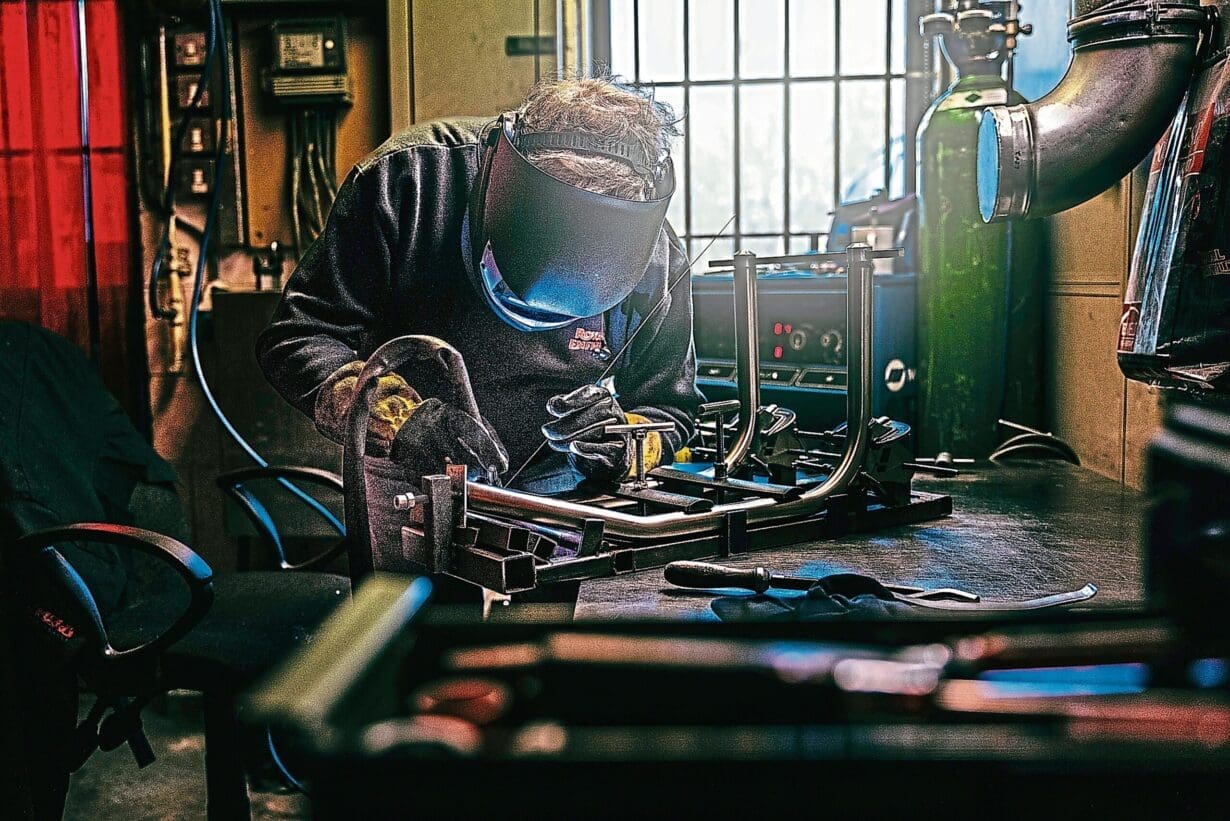
In the early 2000s, Harris partnered with Suzuki to develop its GSX-R750 SRAD in World Superbikes and Honda with its SP-1 in British Superbikes, all the while still working behind the scenes on various projects in GP racing, including the Sauber MotoGP bike (which never saw the light of day) and the WCM MotoGP bike (which used a Yamaha four-stroke engine based on the R1’s). That bike competed in the 2003 and 2004 MotoGP Championship as Harris-WCM in the infancy of the four-stroke era. I could go on about Harris’ credentials when it comes to chassis design but suffice to say, the firm knows its stuff.
Harris’ latest race project is a chassis built to take advantage of the rules in the GP2 class in the British Championship, which is essentially the same as the Moto2 class, but with a free choice on supersport spec engines rather than the spec Triumph engine in Moto2.
Conveniently, an achingly gorgeous chassis from the GP2 bike is in the room where I’m standing with Dominic Ferrer, engineering manager, and Tim Allan, Harris’ senior chassis engineer, who between them have 50 years of experience in the business. I am in the presence of people who have probably forgotten more about motorcycle design and set up than I’ll ever know, so I pin my ears back and start asking questions, using the GP2 chassis right next to us as a starting point, and Dominic and Tim take the lead.
“The GP2 project would have begun in 2018 to enter the championship in 2019, and because it was supposed to be more of a cost-driven race series (GP2), we wanted to use a T45 steel tube front frame – T45 in an aircraft spec alloy, also because it’s more what we’re traditionally known for; we wanted to make it identifiable as a Harris product. So, rather than make an aluminium beam frame, which we have done in the past for a Moto2 project in the world championship, we went with a steel frame at the front which is bronze welded. We’ve done a lot of steel chassis over the years, so we understand the flex and characteristics of the material, but we also wanted to introduce some other techniques to showcase, such as the billet section at the rear, which also helped us develop the chassis faster. If we wanted to change a characteristic, we just had to make a new front section and bolt it in, rather than have to cut up a fabricated item and start all over again. It’s all done on CAD, which helps with understanding where we want the flex, and where we need the strength.
We had the idea of using the engine as a semi-stressed member, but we couldn’t because we used a Yamaha R6 engine. However, most manufacturer’s engines – apart from the Ducati V4 – aren’t stressed members, so you have to accept there are limitations there (in terms of the strength of the engine’s cases), so technically not in a fully stressed way. Production stuff these days is very good, but it is built to a cost, especially with modern castings.
The Achilles’ heel these days in a racing environment is probably the swingarm. The cast swingarms on production bikes are generally very stiff and heavy, which adds to unsprung weight. The majority of the grip a bike generates is from its swingarm; it has a huge effect on the feel and characteristic of the bike. Most machined aftermarket swingarms these days are in the realms of £15k to £20k if you’re using a Suter, Kalex, or one of ours. They’re expensive items, so obviously people aren’t changing them for cosmetic purposes; there is a big performance gain from a lighter, more flexible swingarm. It’s a fundamental part on the whole bike. Wheels are another element. Cast wheels on production bikes have limitations, whereas forged wheels – either magnesium or aluminium – have more flex inherently in them. You generate grip from the tyre, the wheel and the swingarm, and the suspension is doing the last part of the work.
These days we understand that everything contributes to grip. Back in the 500GP days when the understanding really wasn’t there, they were trying to tame bikes that had far too much power and were far too stiff because that was the thinking at the time, so you saw a lot of terrible accidents. The tyre was unable to cope with so much of the load because the chassis wasn’t flexing.
It’s all about management through the whole race to extend tyre life through the flex of the chassis and give greater feedback to the rider. However, we’ve gone full circle to where we are now because the bikes are getting stiffer again, even than they were probably no more than five or six years ago. This is because the electronics are so good on them now that they’re able to compensate for the other factors you were trying to fight before, hence why the Ducati is quite a successful bike. Its engine is a fully stressed member, which makes it a very, very stiff bike. You only have to go back to when Rossi was at Ducati and the struggle he had with trying to get it to build a chassis that had flex, but now they are going stiffer again. It’s not that the electronics are masking a problem; it’s just that they’re managing it in a better way. It’s just the path we are on.
We think electronics will fundamentally change the way chassis are designed in the future. They’ve opened many doors for people to go off and try stuff again that didn’t work before, like carbon frames. Cagiva tried carbon frames in the 1990s because the thinking then was that they had to be really stiff, then back to the present day, and they’re all experimenting with carbon again because there’s a much better understanding of the material, plus we also think they can compromise a bit on packaging and design because the electronics can cope with it. We’re not relying just on mechanical grip anymore at the highest level of prototype racing. On this sort of bike (GP2), we’re still asking just the chassis to create the grip, but when you get to MotoGP, the electronics are coping with much of the stuff you’re asking from the chassis.”